1、应用场景
大型锻件是航空航天、石油化工、交通装备、国防建设、核电核能等行业的基础和关键零部件,在国民经济发展、现代化国家建设、尖端技术开发应用等方面起着举足轻重的作用。
根据我国重机行业的定义,大型锻件是指通过1000t以上水压机生产出的自由锻件,主要生产工序有“炼钢、铸锭、锻造、热处理、粗/精加工”等。生产大型锻件用的钢锭所需钢水达到几百吨,凝固总时长可达100多个小时,不同区域间的冷却速度差异达到100倍以上,钢锭的宏观偏析、缩孔缩松等问题影响巨大。
与中小型锻件相比,大型锻件存在以下问题:(1)其材料流动过程更加难以控制。由于高强钢大型构件的锻件投影面积大、结构复杂,材料的流动距离长,易形成较高的静水压力和表面压力,增加了材料和模腔表面相对流动的摩擦阻力,严重阻碍了材料的流动。此外,锻件温差大,尤其是局部结构特征复杂的区域如突起、枝芽等,材料温度更容易降低,流动更困难,导致锻件难以充满。而且,复杂的结构特征在锻造过程易产生流线紊乱、折叠等缺陷,影响锻件质量;(2)其微观组织演化更加复杂。大型锻件从坯料到锻件,需经历制坯、预锻和终锻的多次加热-变形-冷却过程,特别是其制坯工艺比中小型锻件更复杂,加热-冷却次数更多(甚至达10多道次);锻件内外温度梯度大,不同部位的温差大,微观组织演化(如动/静态再结晶、晶粒长大等)的差别大;锻件不同部位的应变、应变速率差别大,其对微观组织也会产生显著影响。总之,在高强钢大型构件的锻造过程,材料的流动行为及微观组织演化更加复杂难控,极易产生流线紊乱、充填不满等宏观缺陷以及晶粒不均匀、甚至局部异常粗大等微观缺陷。
2、技术优势
针对超大件控形控性难题,燕山大学超大件全流程形性一体化调控团队交叉融合材料、冶炼、材加、力学、机械、数据库等多学科,结合理论分析、数值模拟、实验研究多种手段,研究超大件全流程制造中成分、组织、工艺与性能的内在联系,建立成分、组织、工艺与性能多元数据驱动的超大件全流程制造的专家知识数据库,结合现代机器算法,实现海量数据中专家知识智能获取,为超大件的智能制造技术提升提供新的思路与方法。
团队在大型锻件锻造/热处理工艺关键技术,航空模锻件材料组织演化与性能控制,超大件热处理过程残余应力与形变控制,动态原位分析与高通量全域组织表征,金属凝固成形的传热形变多场协同控制具有长期的技术积累和优势。特别在动态原位分析与高通量全域组织表征方面,在国内具有领先优势。
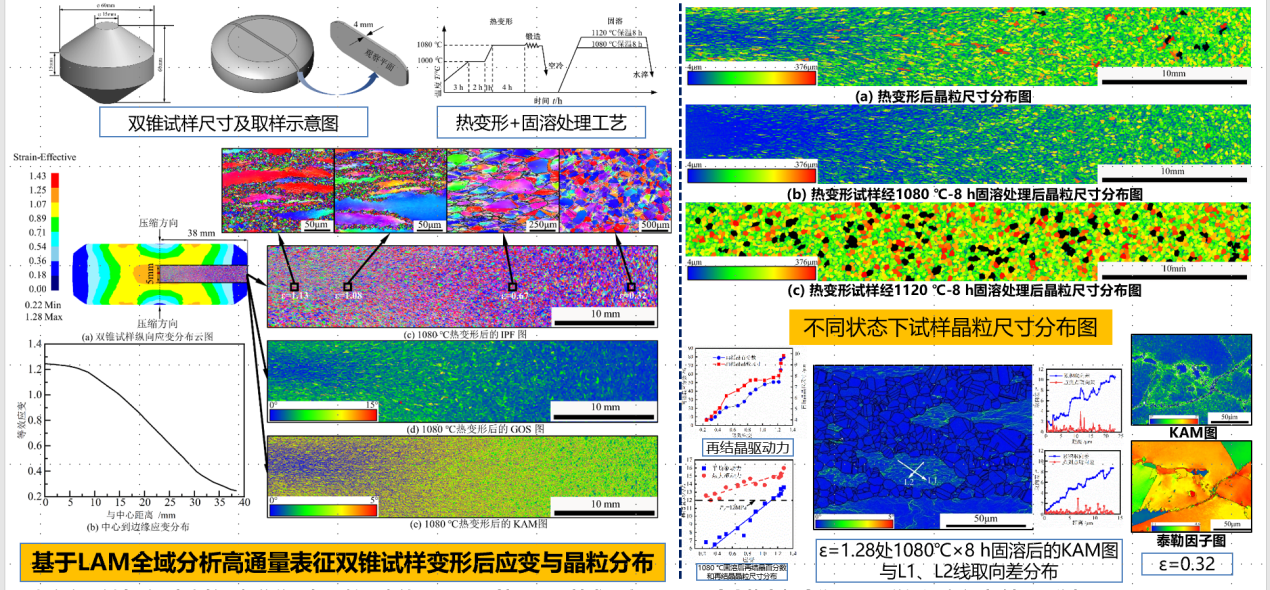
高温合金热加工全流程晶粒演化定量控制
3、关键问题
以上技术成果均由燕山大学刘鑫刚教授带领科研团队独立主持完成,主要面向并解决的是超大件全流程形性一体化调控难题。相关成果已经应用于GH4698/GH4742涡轮盘锻件工艺开发、TC18/TC21钛合金模锻件组织控制与工艺优化、超超临界转子用钢材料与工艺开发、核电主管道全流程组织控制与工艺优化、航空模锻件/叶轮产品热处理形变工艺优化、钢锭凝固缺陷模拟预测与锻造工艺优化等,为大型锻件的高性能智能制造提供了理论基础和技术支撑。